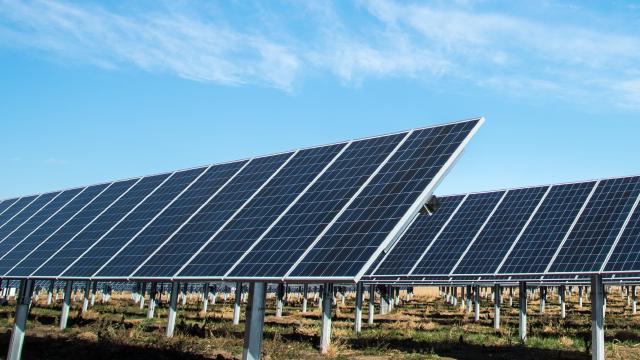
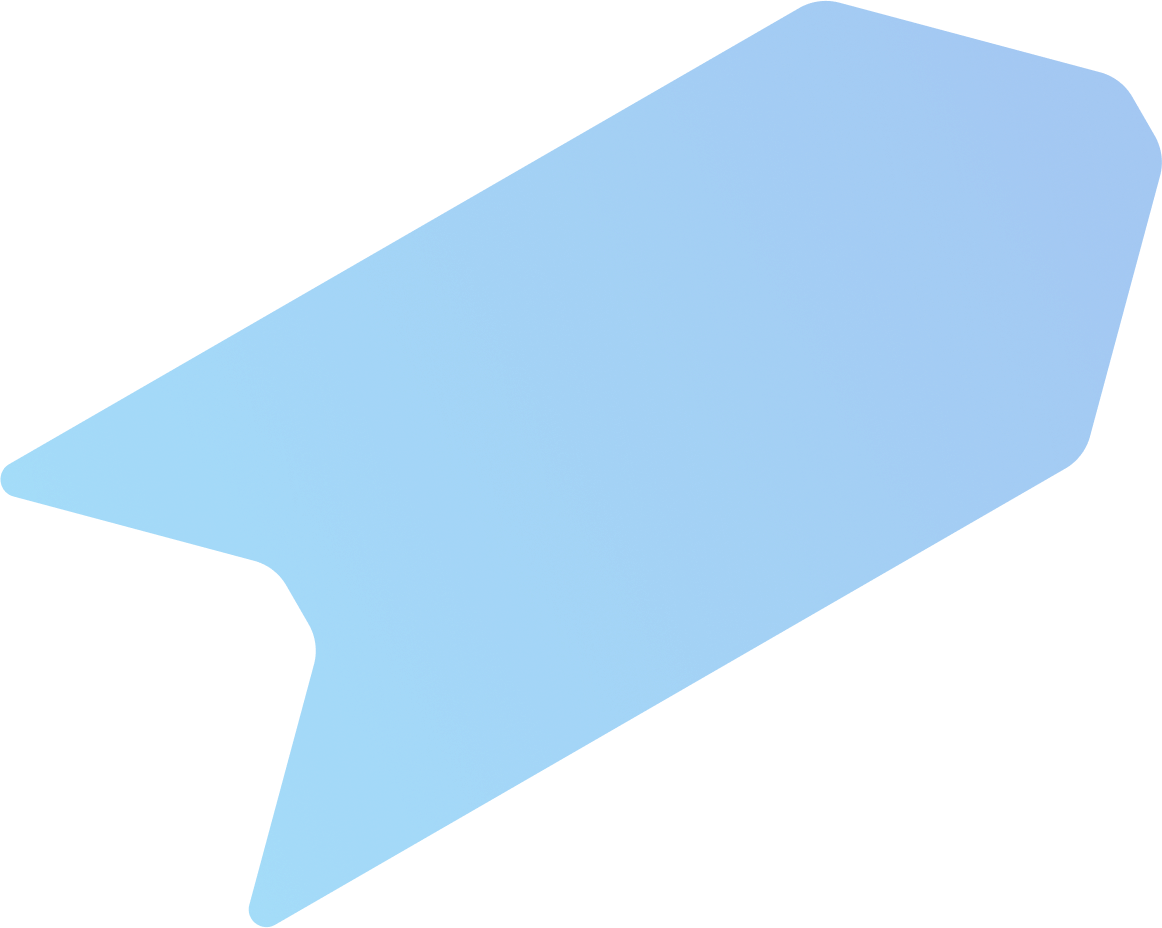
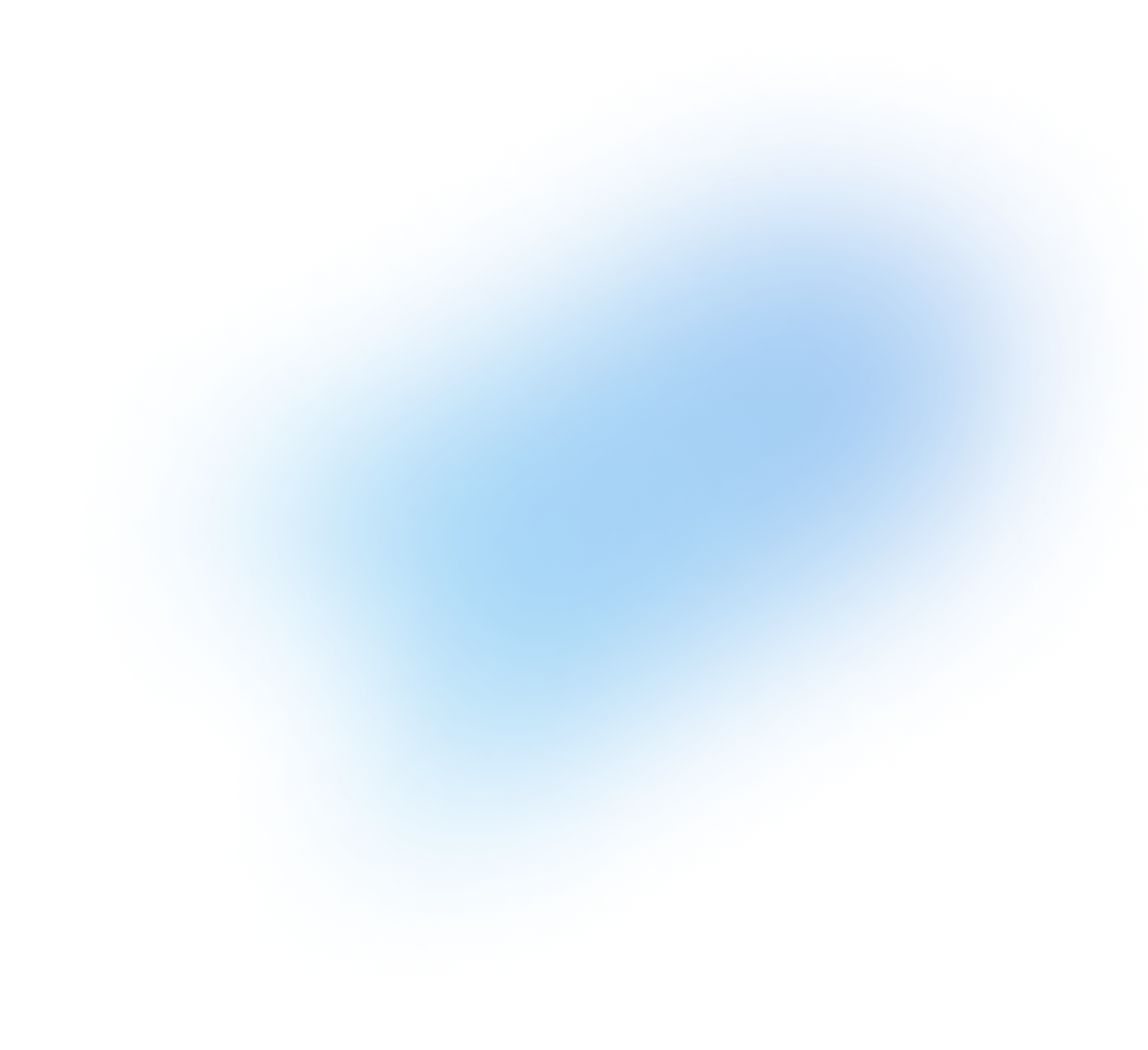
CASE STUDY
Food Supply Chain Optimization Project
Succeeded in minimizing out-of-stock inventory and unsold food at the same time by comprehensively analyzing the data from manufacturers, wholesalers, and retailers
Project Year: 2020
Client: Mitsubishi Shokuhin Co., Ltd.
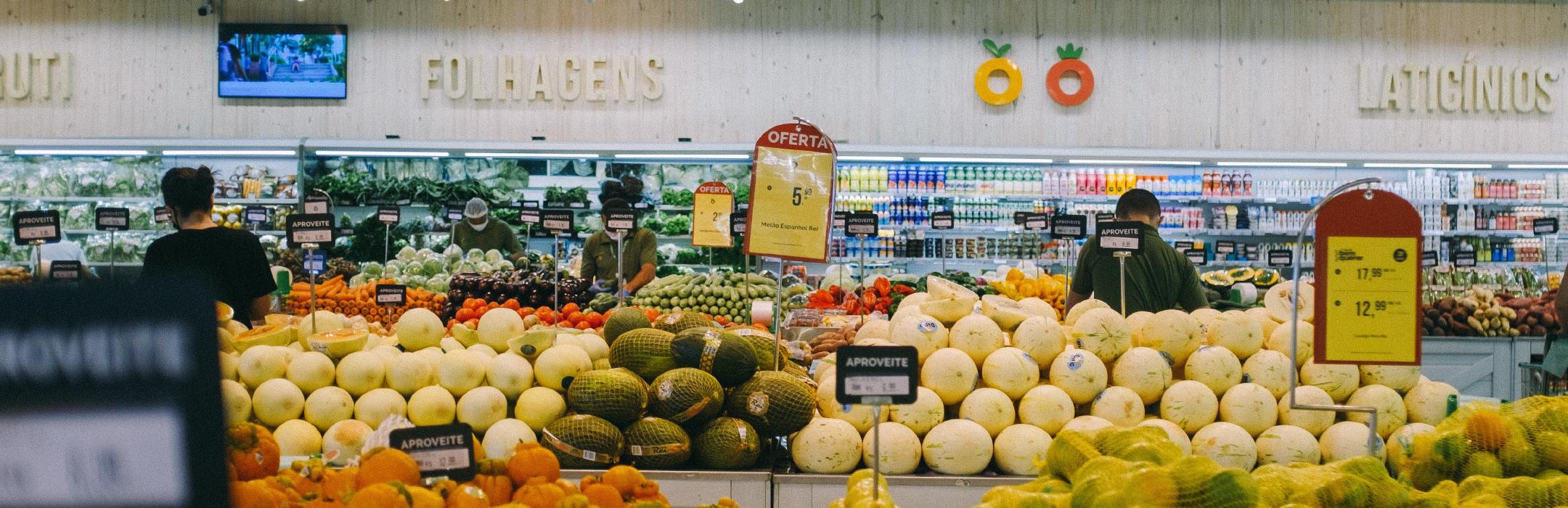
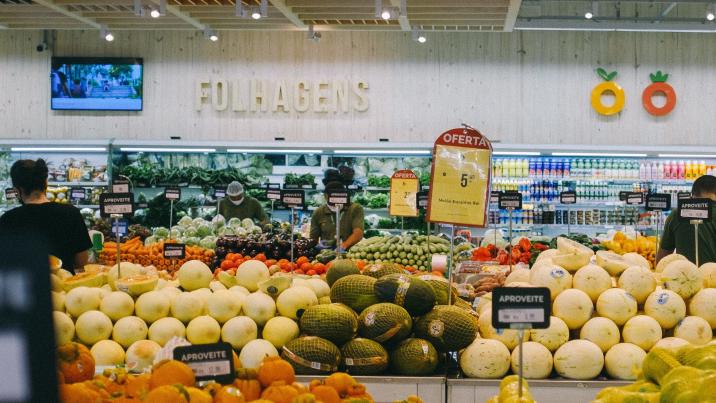
*This content is based on the PoC conducted in 2020.
The Environment surrounding the Food Distribution Industry
Food loss in the food distribution industry has become a major social issue. It is said that the lost value amounts to 1 trillion yen per year. This occurs primarily in the distribution process and is caused by improper food management. Examples include overproduction of food based on incorrect demand forecasts and expiration of shelf life as a result of excess inventory.
Food loss is included in the SDGs as an area of focus and is one of the most pressing issues that needs to be solved quickly on a global scale.
Issue
One of the causes of food loss is the division of information among food manufacturers, wholesalers, and retailers. Since each player decides the number of sales and orders at its discretion and judgment, the deviations from each player’s forecasts add up, resulting in a lot of excess food. For example, when a retailer plans the sale of a particular product, the food wholesaler will increase its inventory in advance to ensure an adequate supply. If actual sales fall short of the forecasts, a large amount of inventory remains, creating the potential for food loss due to the expired shelf life. When a food manufacturer releases a new product, it is particularly difficult to forecast the sales volume because there is no track record to rely on. If a retailer does not have enough space to sell the new product, the risk of having a large inventory increases. In order to resolve the issue of food loss, we need to eliminate this division of information and optimize production and orders throughout the supply chain.
An Approach to Solving the Issue
- our aim was to optimize the entire distribution system in the food industry by comprehensively analyzing the data on orders placed and received and the inventory throughout the supply chain.
- When we first started the PoC, the accuracy of the forecasts showed no sign of improvement, and it was far from practical to use. To respond to the situation, we took advantage of the general trading company’s network to collect a wide range of data not only from the Group companies but also from our business partners. We trained the AI not only on sales data from stores but also on a wide variety of data, including the number of products shipped from warehouses and the time required for procurement. As a result, we are now able to estimate the appropriate level of inventory where the fluctuation in sales volume is also taken into consideration.
Effect
- In the demonstration experiment of approximately 10,000 products, we succeeded in reducing inventory in the distribution center by an average of approximately 30% (or up to 40% in some categories).
- In general, the stockout rate and inventory reduction are inversely related. However, we succeeded in reducing both the stockout rate and inventory at the same time.
- It is estimated that if the inventory of all products handled by Mitsubishi Shokuhin were reduced by 30% to 40%, 300 tons of food loss could be reduced.
- By solving the food loss issue, a reduction of CO2 emissions from food delivery can also be expected.
- MCD developed its own AI engine based on the knowledge obtained from this PoC (patent pending). Mitsubishi Corporation established and led a project to develop an inventory optimization solution for customer companies, and this engine was adopted as the demand forecasting function. Currently, Industry One, Inc., assumes responsibility for project promotion as the PMO. Industry One, Mitsubishi Corporation, and MCD are jointly promoting the application and expansion of the use of this solution for customers’ distribution centers.
Project Members
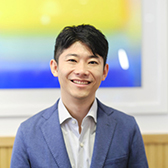
Rei Kubonaga
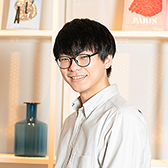
Masahiro Ogino