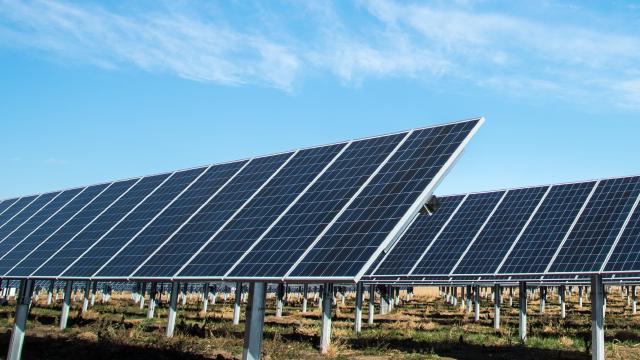
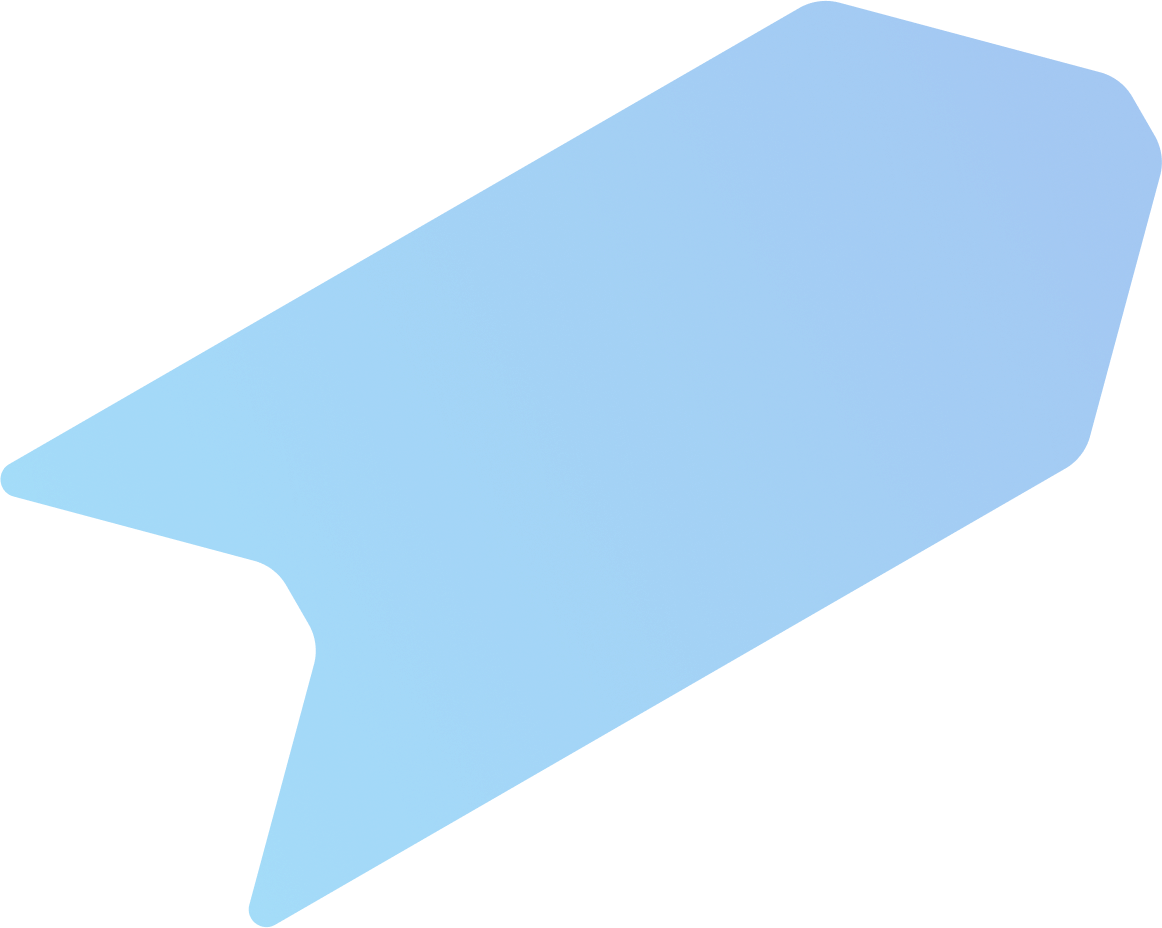
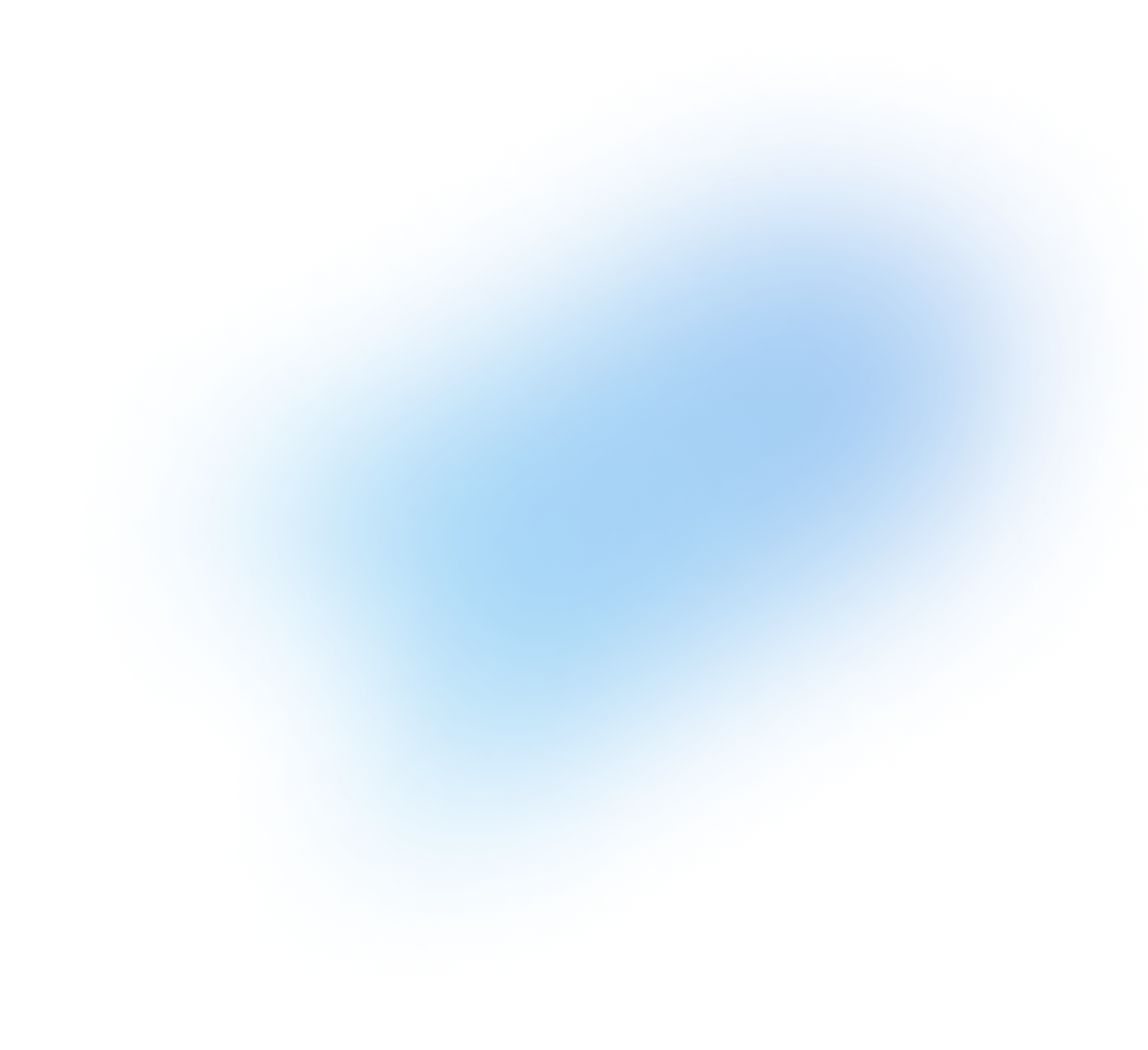
CASE STUDY
Operations Improvement Project at a Mining Site
An Initiative to Optimize the Number of Trucks to Improve Production Efficiency
Project Year: 2021
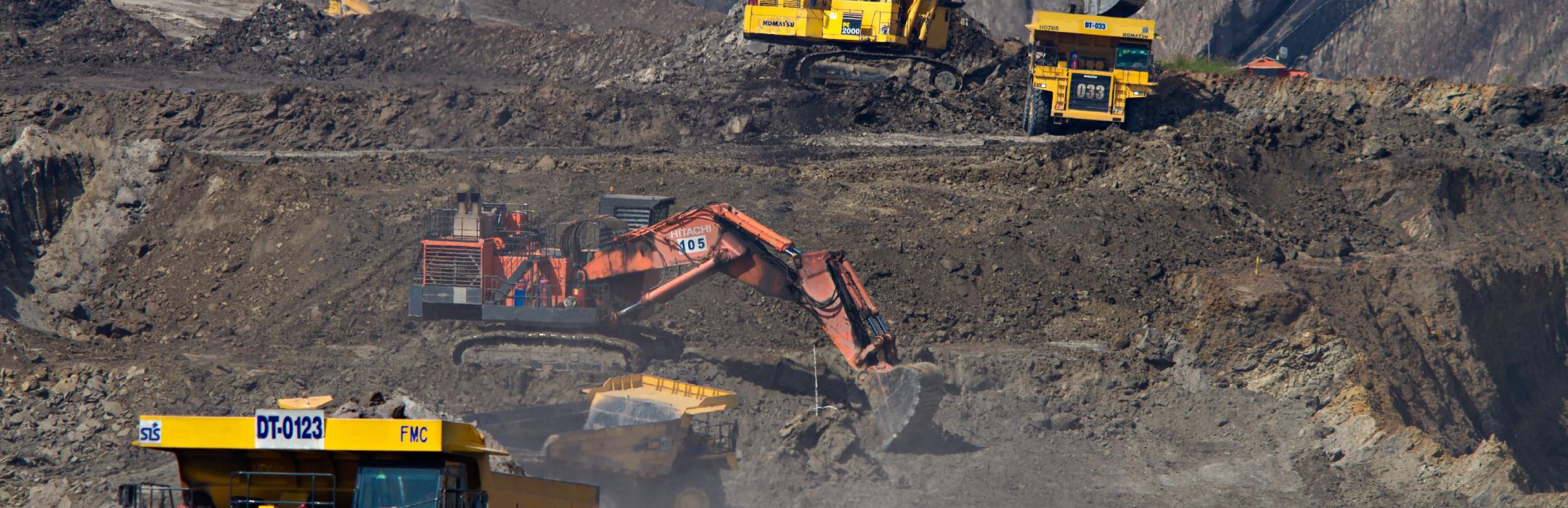
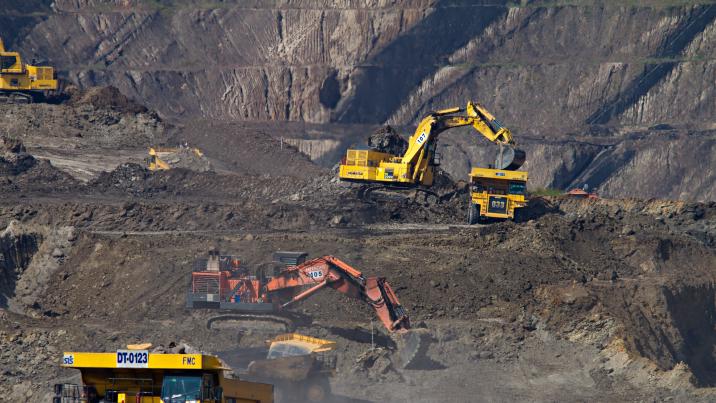
Issue
An operation at a mining site is a complex combination of mining and the transportation of mineral resources.
First, mineral resources are mined at a mining site using mining machines. The mined resources are then loaded onto trucks. The trucks transport the resources from the mining site to the unloading site where the resources are unloaded. When this series of transportation operations is complete, the trucks return to the mining site to collect the mined resources again. In this way, the mining operation consists of a repetition of the work done by mining machines and trucks.
The number of trucks in operation plays an important role in improving the efficiency of mining operations.
For example, if there are no trucks waiting at a mining site, the mining machine cannot load the mined resources onto trucks; therefore, the operation will be forced to stop. Conversely, if more than one truck is waiting, they have to wait to receive the mined resources.
There has been an issue at the mining site that such inefficiency in arranging the trucks is causing a loss of opportunity.
An Approach to Solving the Issue
We tackled this issue in two stages: building a model to estimate the production volume of mined resources and then maximizing the production efficiency using the output of the model.
Production Volume Estimation Model
- We calculated the time required for a truck to travel back and forth between the mining machine and the unloading site and the time required for the mining machine to load the mined resources onto the trucks. We then entered the results into the Queueing Theory model to estimate the production volume.
- We also built a model to correct errors between the output of the production volume estimation model and the actual measured value by using machine learning, and incorporated it into the production volume estimation model. This allowed us to build a more accurate model based on the combination of the mathematical model and machine learning.
Maximizing Production Efficiency
- To maximize production efficiency, we developed an algorithm to calculate the optimal number of trucks.
- We calculated the production volume per truck from the output of the production volume estimation model and used the greedy algorithm, a type of algorithm effective when solving optimization problems, to calculate the number of trucks that maximizes production efficiency.
Data used
- Production volume data
- Data of mining machine and truck operations
Effect
- The following result was obtained by dividing the values after optimization by the actual values of production volume and cost for each day during a given period of time and plotting the resulting values in the box-and-whisker plot.
- For almost all days during the period, it was found that the production volume increased (one or more) and the costs decreased (one or less) when compared to the actual values.
- Looking at the whole period, it was found that there was potential to simultaneously increase the production volume by 9% and reduce costs by 5%.
- We are currently exploring the potential for practical application and investigating its application to other resource mining sites.
Project Members
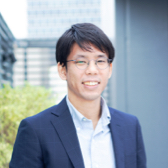
Yusuke Nakata